Das Ergebnis einer Spulenwicklung
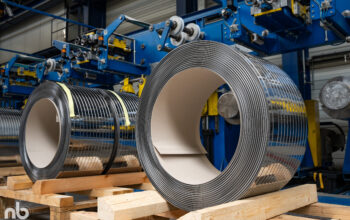
Erinnert ihr euch noch an unseren Post: „Länge läuft“?
Heute wollen wir euch mitnehmen auf eine Reise von Kiel, auf der A7 Richtung Süden, bis nach München. Immerhin eine Strecke von ca. 880 km. Wir möchten hier versuchen, euch etwas näherzubringen, was das mit unseren Produkten zu tun hat. Doch bevor wir starten, eine Frage: Wisst ihr eigentlich, wie dick ein Geldschein oder ein 1-Cent-Stück ist?
Dabei ist es egal, welcher Betrag auf dem Schein steht, denn die Dicke aller Geldscheine ist identisch. Unsere Geldscheine sind nur 0,10 mm dick. Unsere 1-Cent-Stücke sind mit einer Dicke von 1,67 mm fast schon dick. Wir zeigen euch heute ein hier gefertigtes Produkt, was auch wir bislang so noch nicht hergestellt haben. Ihr werdet zugeben müssen, das ist schon wirklich etwas Besonderes.
Genau so dick wie 3 dieser 5-Euro-Scheine, oder besser gesagt so dünn, war das Band, das wir für einen unserer Kunden geschnitten haben. Sportlich, aber noch nicht sportlich genug? Kein Problem, dann setzen wir noch einen drauf. Das Band war nicht nur 0,3 mm dünn, sondern auch nur 5 mm breit. Also gerade mal so breit, wie drei aufeinander gestapelte 1-Cent-Stücke.
Immer noch nicht genug? Auch da können wir noch etwas dazu legen. Und dann sind wir beim Thema „Länge läuft“. Auf dem Bild seht ihr eine hier hergestellte Spule. Ein Streifen mit einer Stärke von 0,3 mm und einer Breite von 5 mm. Dort haben wir in oszillierender Wicklung diesen einen Streifen über eine Breite von 300 mm insgesamt 47-mal nebeneinander liegend aufgewickelt. Wieder und wieder, bis der erste Einsatzstreifen aufgebraucht war.
Und weil wir das nicht nur mit einer Spule perfekt beherrschen – sondern gleichzeitig mit 20 Spulen auf unserer Maschine 11, einem 20-fach Spuler, der jeweils zwei Spulen gleichzeitig und das Ganze zehnmal hintereinander aufnehmen kann – haben wir uns das getraut. Eingesetzt haben wir dafür ein Werksbreitband mit 1250 mm Einsatzbreite. Das haben wir in 14 schmalere Streifen vorgespalten und dann jeweils in 20 Spulen in einer Fertigbreite von 5 mm gespalten. Diese 14 Vorspaltbänder haben wir dann nacheinander auf die Anlage genommen und nach jedem Bandende den nächsten Vorspaltstreifen mit unserer Laser-Schweißanlage mit dem vorherigen verschweißt.
Herausgekommen sind somit 20 Spulen, die durch jeweils 13 Schweißstellen verbunden und dann weiter aufgerollt worden sind. Durch diesen Prozess haben wir jetzt eine sogenannte Packenwicklung erzeugt, die jeweils aus einer einzigen Ader besteht und die durch diese Verlängerung eine beachtliche Länge erreicht hat. Es sind fast auf den Punkt genau 44.000 Laufmeter, die jetzt auf jedem dieser 20 Packenwicklungen gewickelt wurden.
Und weil wir das insgesamt 20-mal gleichzeitig gemacht haben, kommen wir so auf die beachtliche Länge von 20 x 44.000 Metern oder von gut 880 km. Würden wir einen Bandanfang in Kiel am Ortsschild festbinden und dann nach Süden fahren, dabei die Packenwicklungen nacheinander abrollen und immer miteinander verbinden, würde der letzte Bandmeter ohne Unterbrechungen in München von der letzten der 20 Packenwicklungen laufen.
Ihr habt im vorherigen Post gelesen, dass solch schmale Abmessungen nicht besonders hoch gewickelt werden können. Darum hätte ein Einzelring einen vergleichbaren Außendurchmesser, wie die Spule hier von der Seite betrachtet.
Der Kunde hätte somit anstelle einer Packenwicklung dann etwa jeweils 47 Einzelringe pro Palette erhalten. Bei 20 Packenwicklungen wären das gut 940 Einzelringe gewesen, die er bei sich alle einzeln auf seine Fertigungsanlage hätte nehmen müssen. Viel Arbeit, Zeit und Geld, die ihn das gekostet hätte.
Jetzt setzt er eine Spule auf seinen Automaten und startet den Betrieb.
Es ist schon ein erheblicher Unterschied, ob der Kunde nun eine Spule aufsetzt und dann störungsfrei bis zu tagelang fertigen kann, oder ob er immer wiederkehrende Umrüstungen durchführen muss.
Und darum nochmals: Länge läuft…
______________
Do you remember our post: „Length runs“?
Today, we want to take you on a journey from Kiel, down the A7 southbound, all the way to Munich. That’s a distance of about 880 km. We’d like to try to explain how this relates to our products. But before we start, a question: Do you know how thick a banknote or a 1-cent coin is?
It doesn’t matter which denomination is on the note, because all banknotes have the same thickness. Our banknotes are only 0.10 mm thick. Our 1-cent coins are almost thick at 1.67 mm. Today, we will show you a product manufactured here that we haven’t produced in this form before. You’ll have to admit, it’s really something special.
The strip we cut for one of our customers was exactly as thick as three of these 5-euro banknotes, or rather, as thin. Impressive, but not impressive enough? No problem, we can go further. The strip was not only 0.3 mm thin but also only 5 mm wide. That’s just as wide as three stacked 1-cent coins.
Still not enough? We can add more. And that brings us to the topic „Length runs“. In the picture, you see a spool manufactured here. A strip with a thickness of 0.3 mm and a width of 5 mm. We wound this one strip a total of 47 times side by side over a width of 300 mm using oscillating winding. Again and again until the first insert strip was used up.
And because we not only master this perfectly with one spool but simultaneously with 20 spools on our machine 11, a 20-fold spooler that can simultaneously accommodate two spools and do this ten times in succession, we dared to do it. For this, we used a millcoil with a width of 1250 mm. We slit this into 14 narrower strips and then into 20 spools with a finished width of 5 mm each. We then took these 14 pre-splitted bands one after the other on the machine and weld each subsequent pre-splitted strip to the previous one with our laser welding system after each strip end.
The result is 20 spools, connected by 13 welds each and then re-rolled. Through this process, we have now created what is called anoscillated winding, consisting of a single strand that, due to this extension, has reached a considerable length. It’s almost exactly 44,000 running meters wound on each of these 20 oscillated windings.
And because we did this simultaneously 20 times, we achieve the impressive length of 20 x 44,000 meters , or let’s say 880 km. If we tie the start of the strip to the town sign in Kiel and drive south, unwinding the package windings one after the other and always connecting them, the last meter of the strip would run from the last of the 20 oscillated windings in Munich without interruptions.
You read in the previous post that such narrow dimensions cannot be wound very high. Therefore, a single ring would have a comparable outer diameter to the spool viewed from the side here.
The customer would thus have received about 47 individual rings per pallet instead of anoscillated winding. With 20 oscillated windings, that would be about 940 individual rings, which he would have had to load individually onto his production line. A lot of work, time, and money it would have cost him. Now he puts a spool on his machine and starts working.
It makes a significant difference whether the customer installs one spool and can produce smoothly for up to several days, or whether he has to perform recurring coil installations.
And that’s why, once again: Length runs…